Water and Environment
There are few industries as diverse as the water and environmental industry. Here, KELLER Pressure sensors can be found in all manner of applications. For instance, they are used to measure the sea depth, monitor the water pressure at the bottom of dams, calculate flow quantities and regulate water levels. Thanks to its many years of experience, KELLER Pressure can offer broad expertise in these areas.
Filters
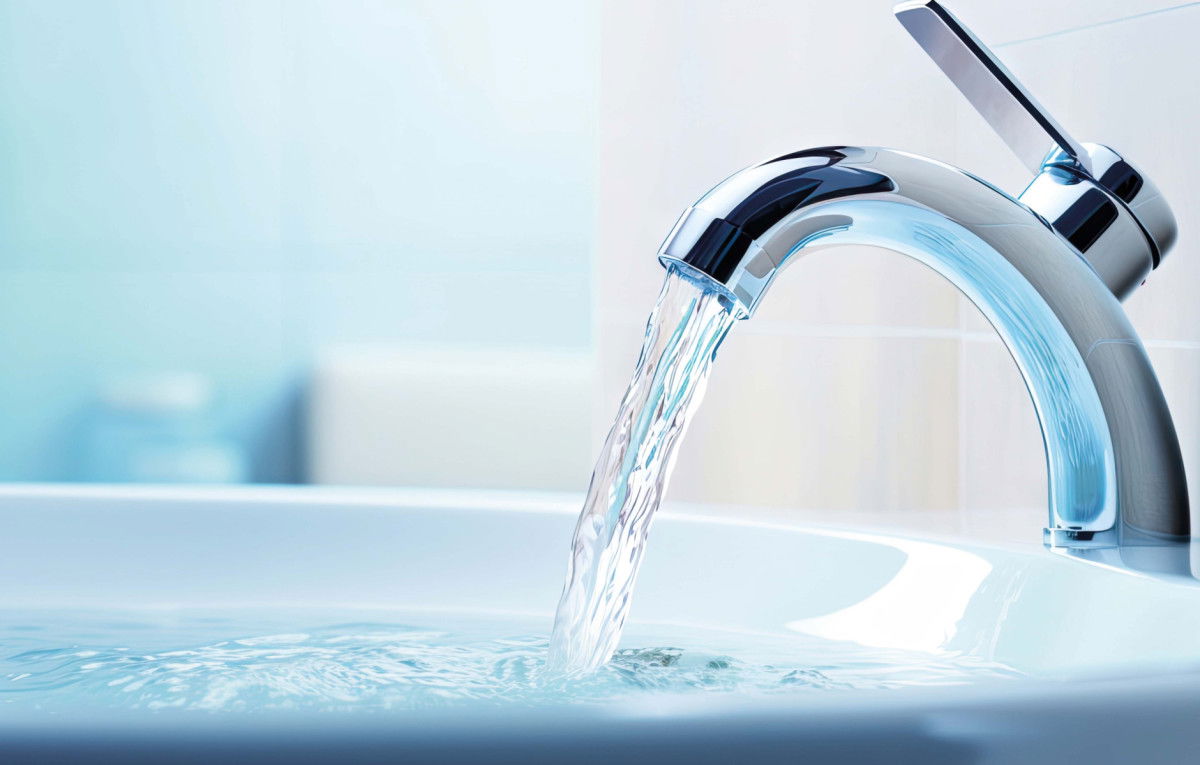
Without Water Everything Comes to a Halt
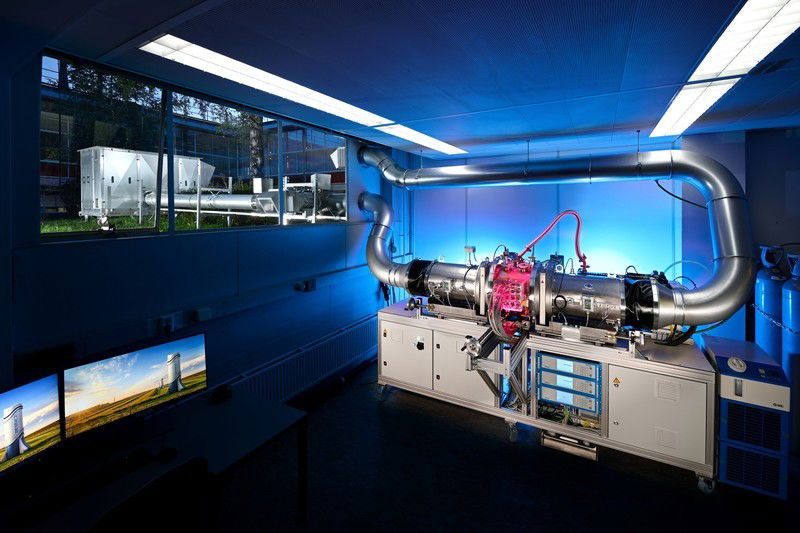
CO2 Recycling
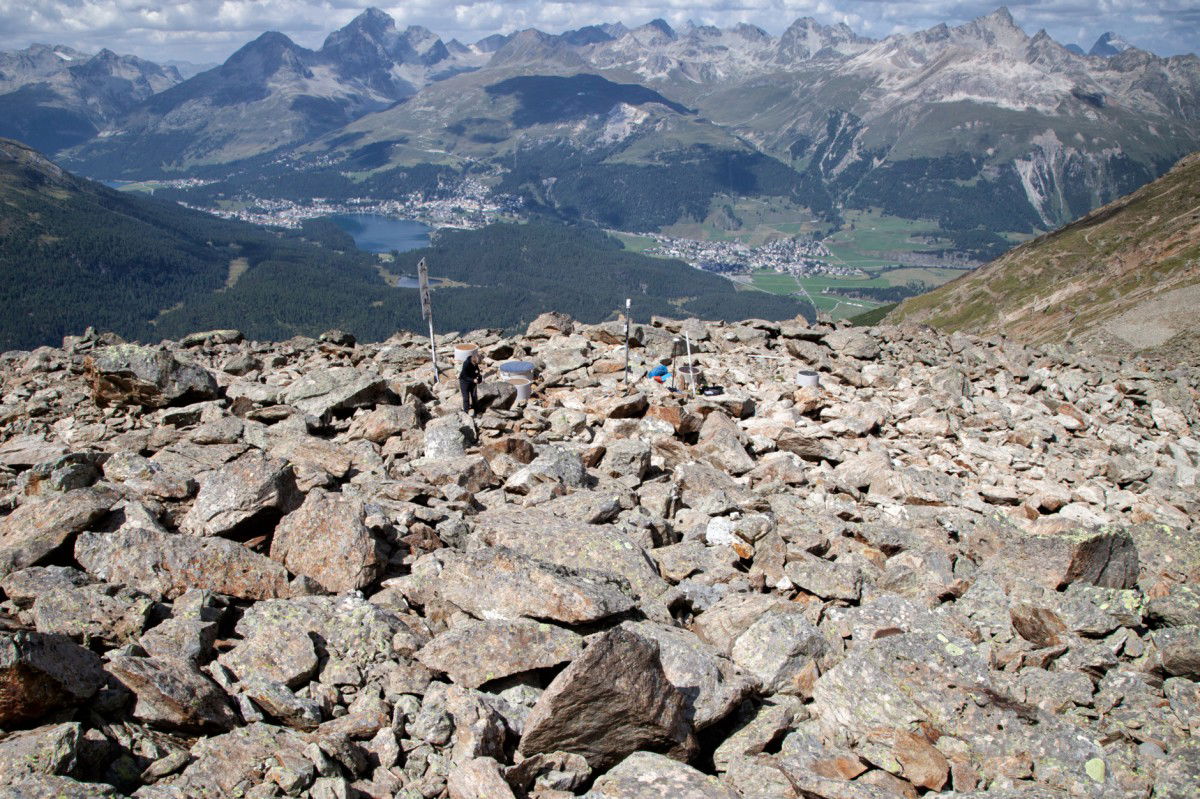
Pore-Water Pressure Monitoring in Ice-Rich Permafrost
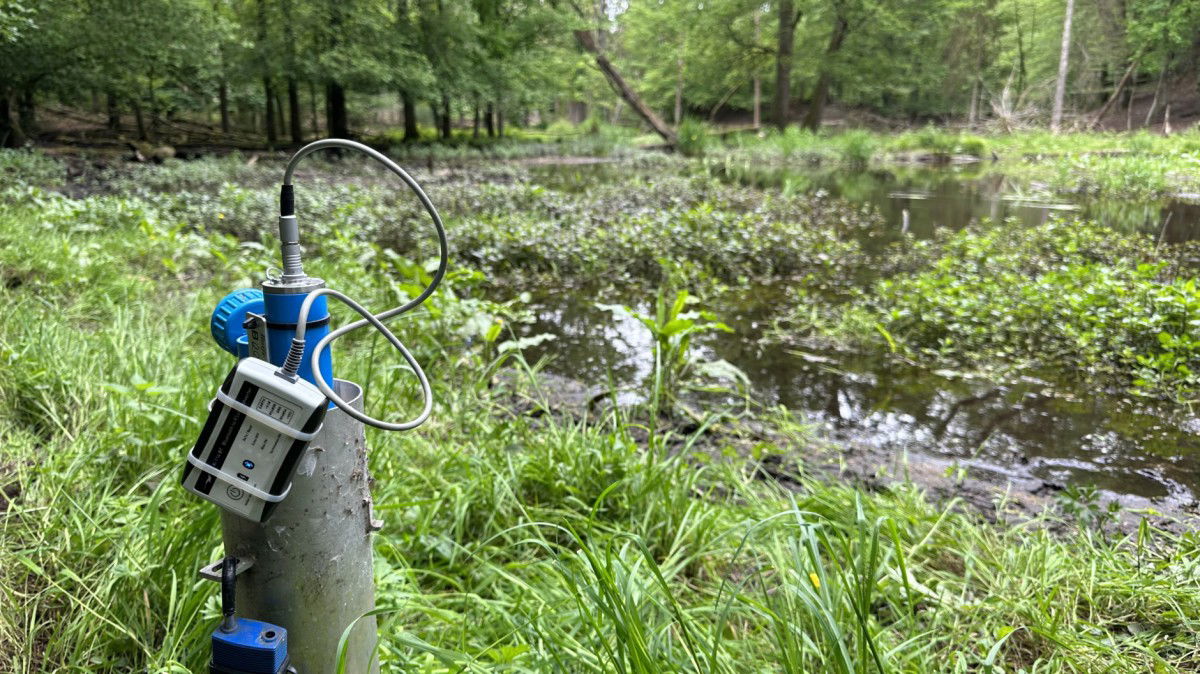
Upcycling Sensors
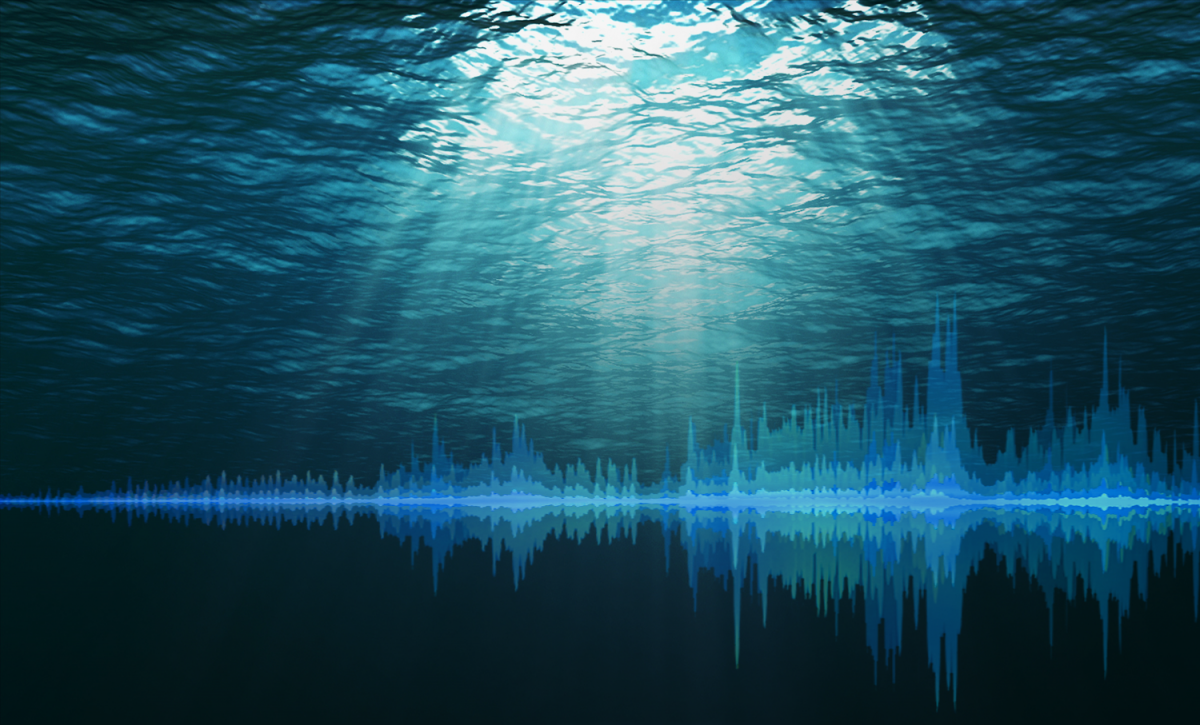
Monitoring the Seabed – The Subtle Distinction
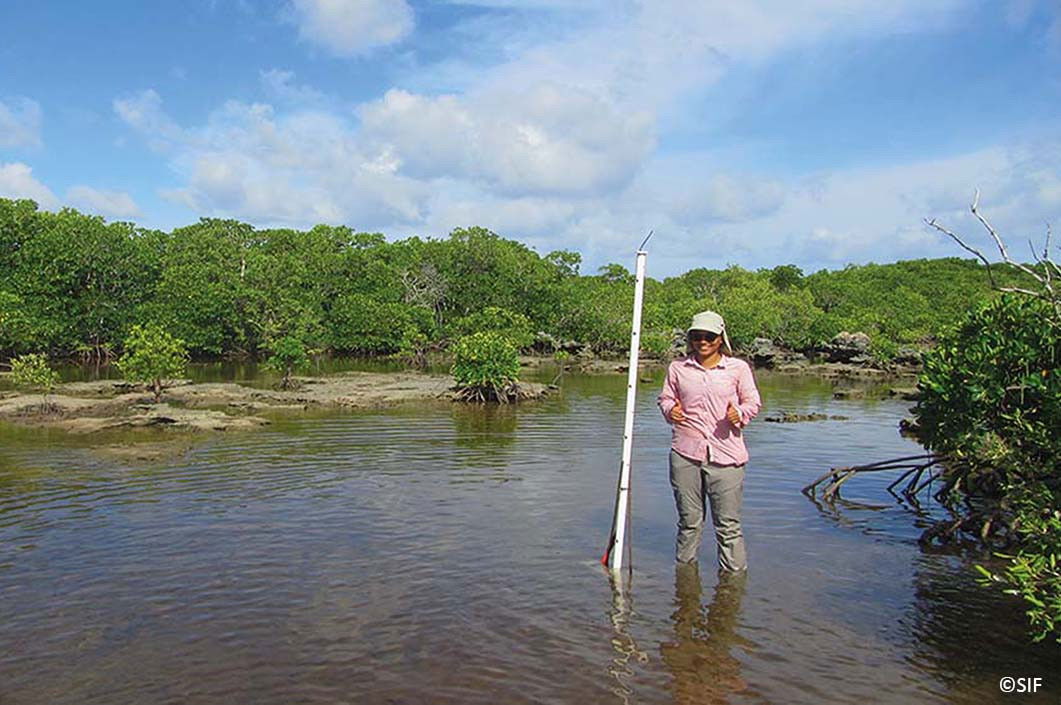
How to Measure the Pressure on our Eco-System
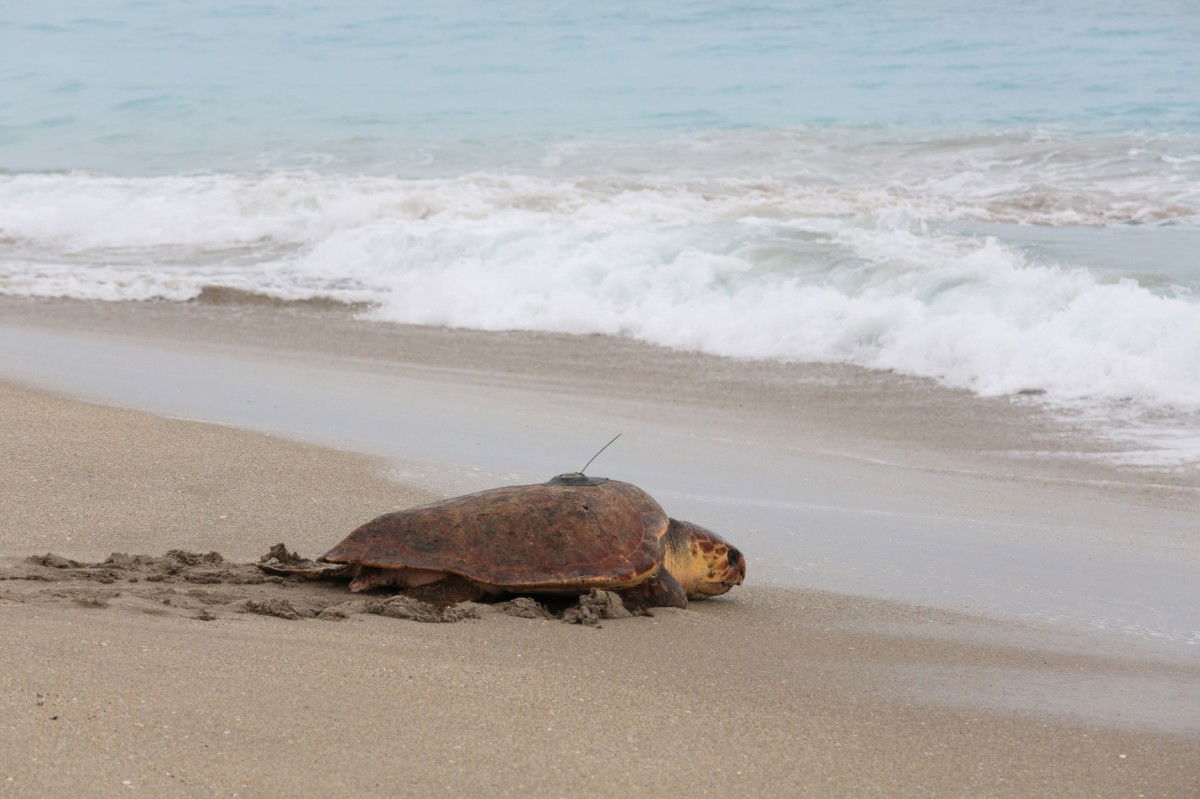
Tracking Devices for Marine Animals
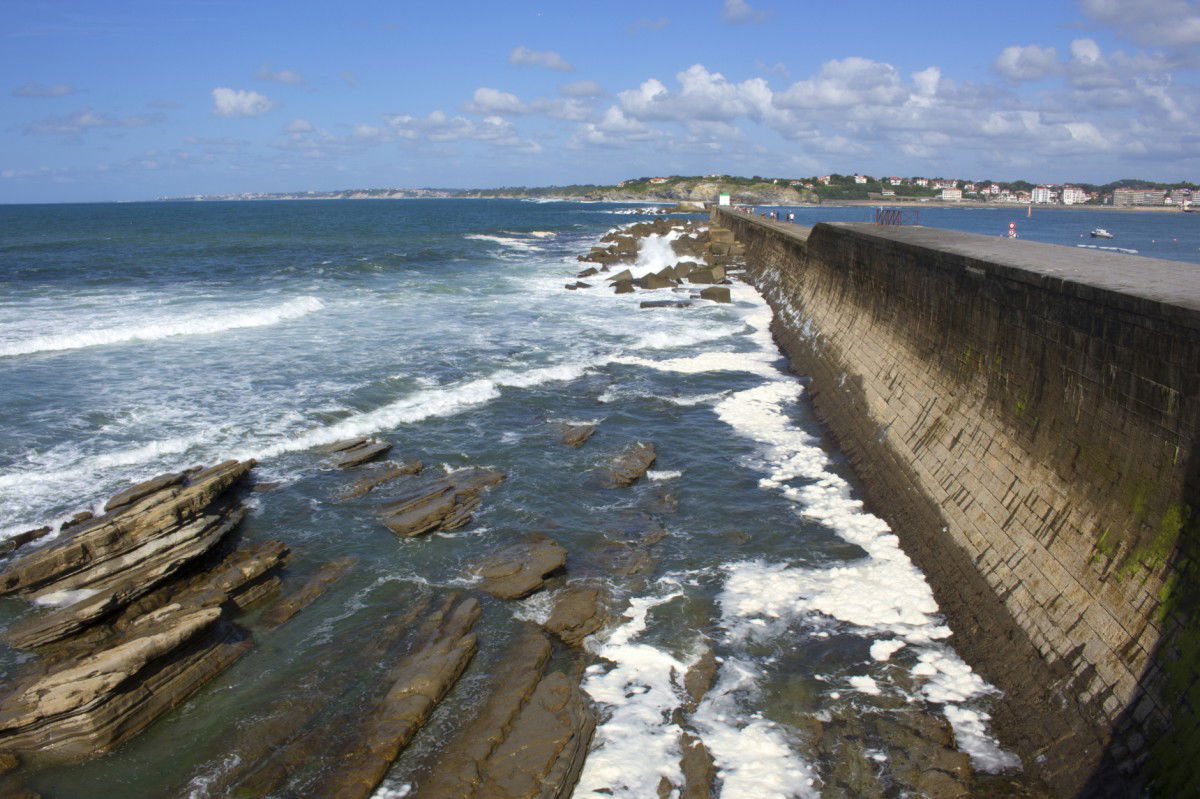
Measuring Wave Impact Pressure
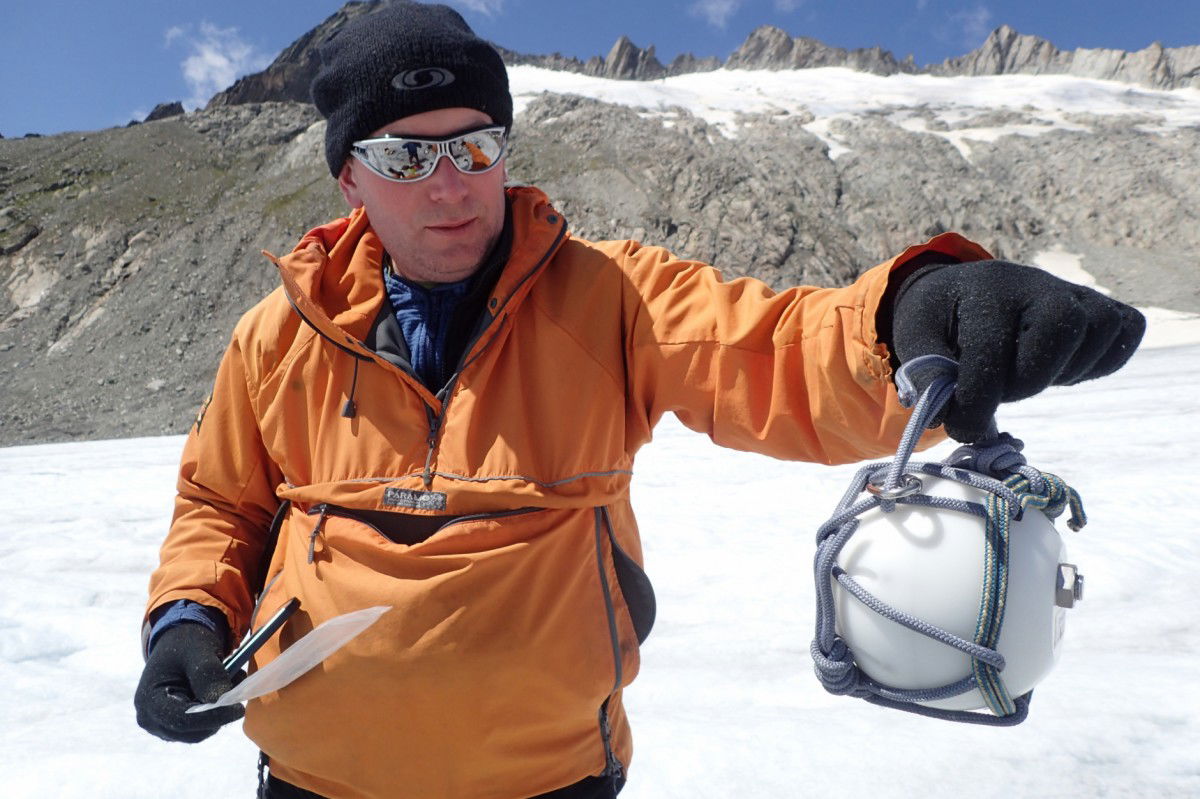
Cryoegg Glacier Research
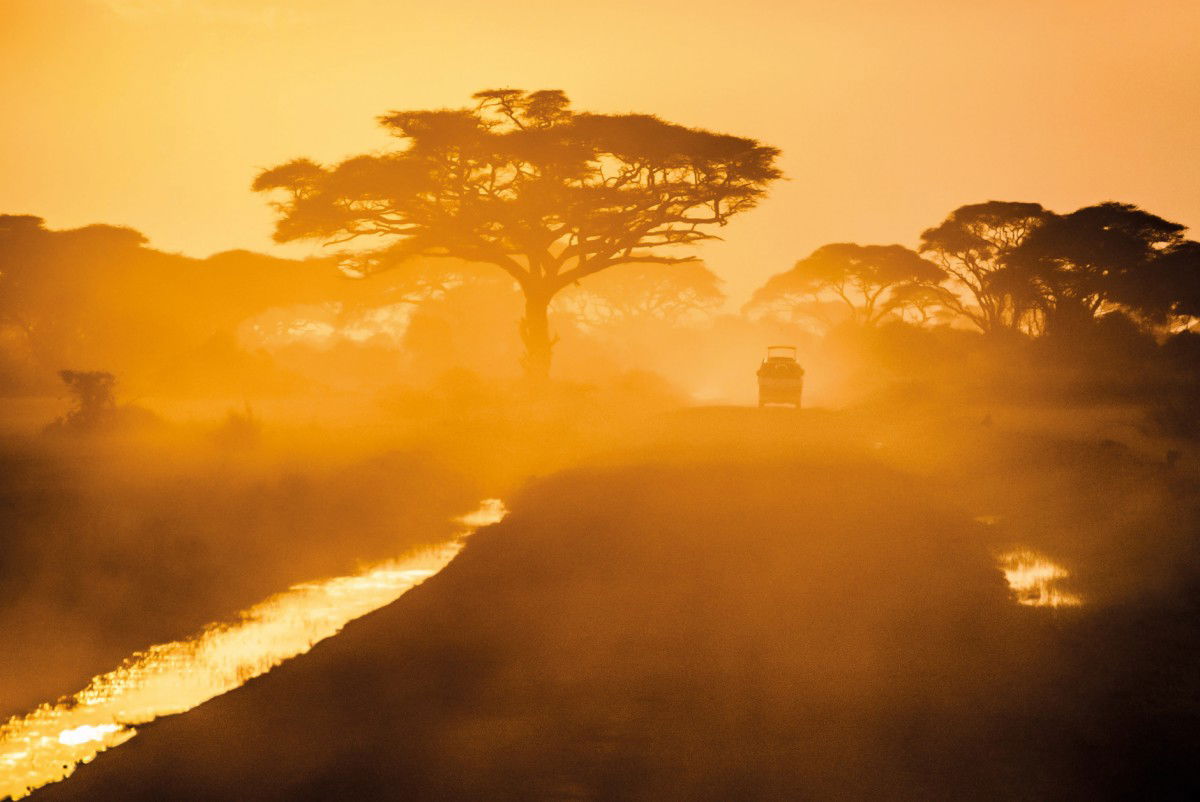
Kololo’s Water System
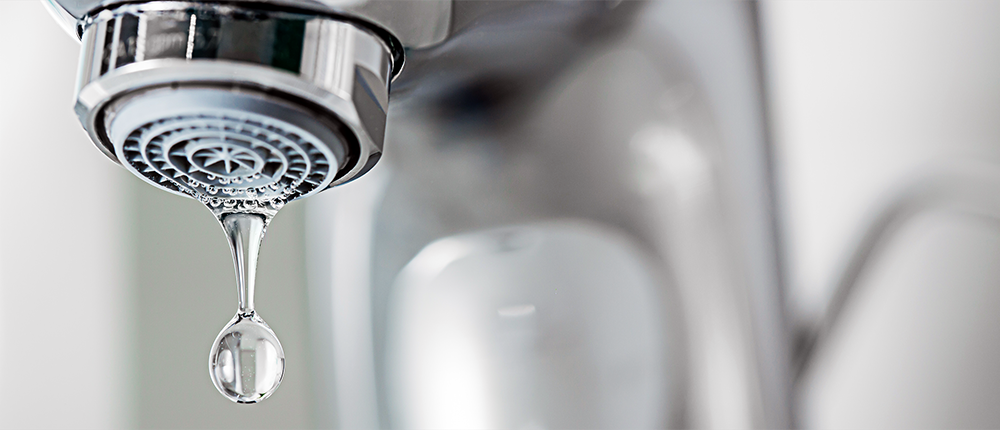
Reducing Drinking Water Losses
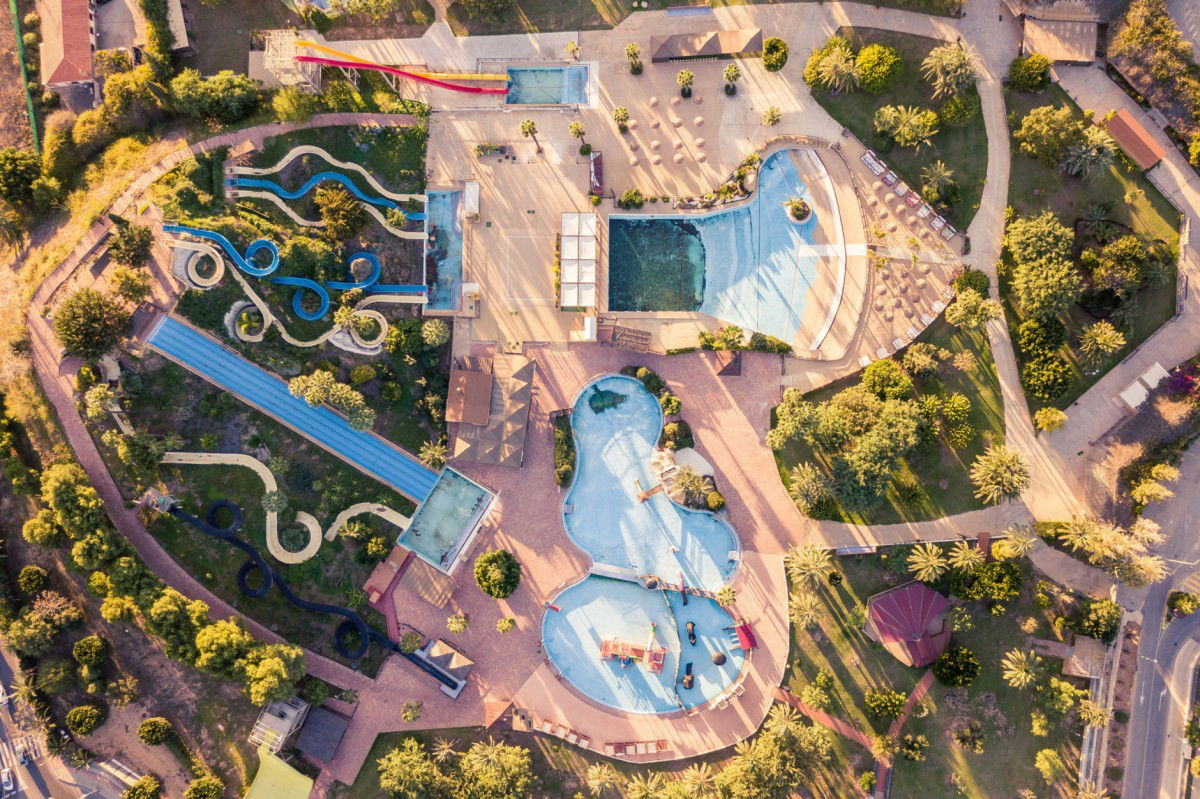
Hydraulic Network Analysis
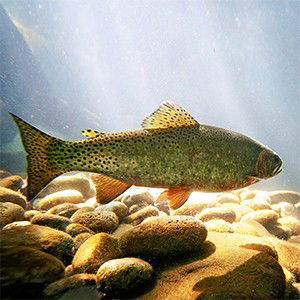
Fish Farm Water Level Monitoring
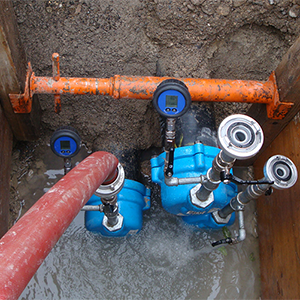
Pressure Sensors on Water Pipelines
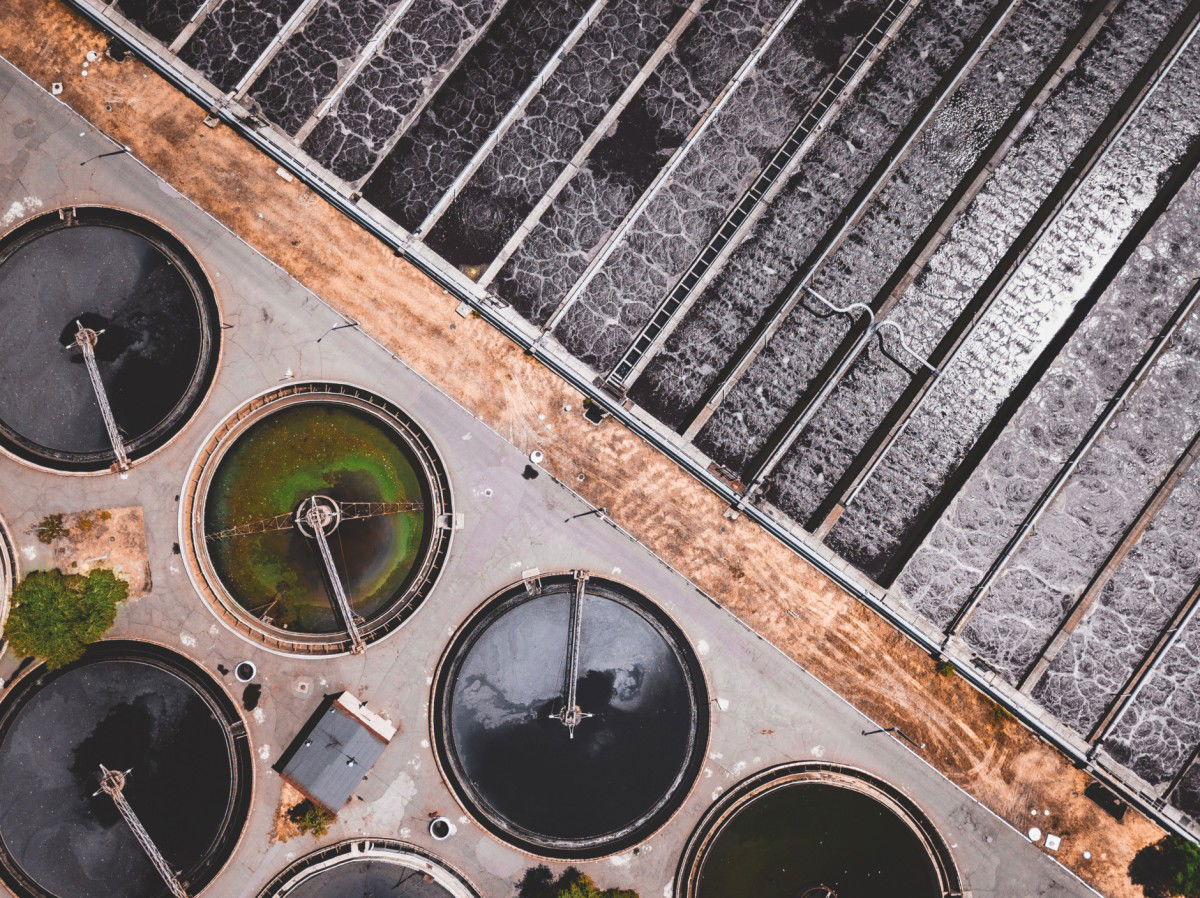
Intelligent Sewage Overflow Measurement
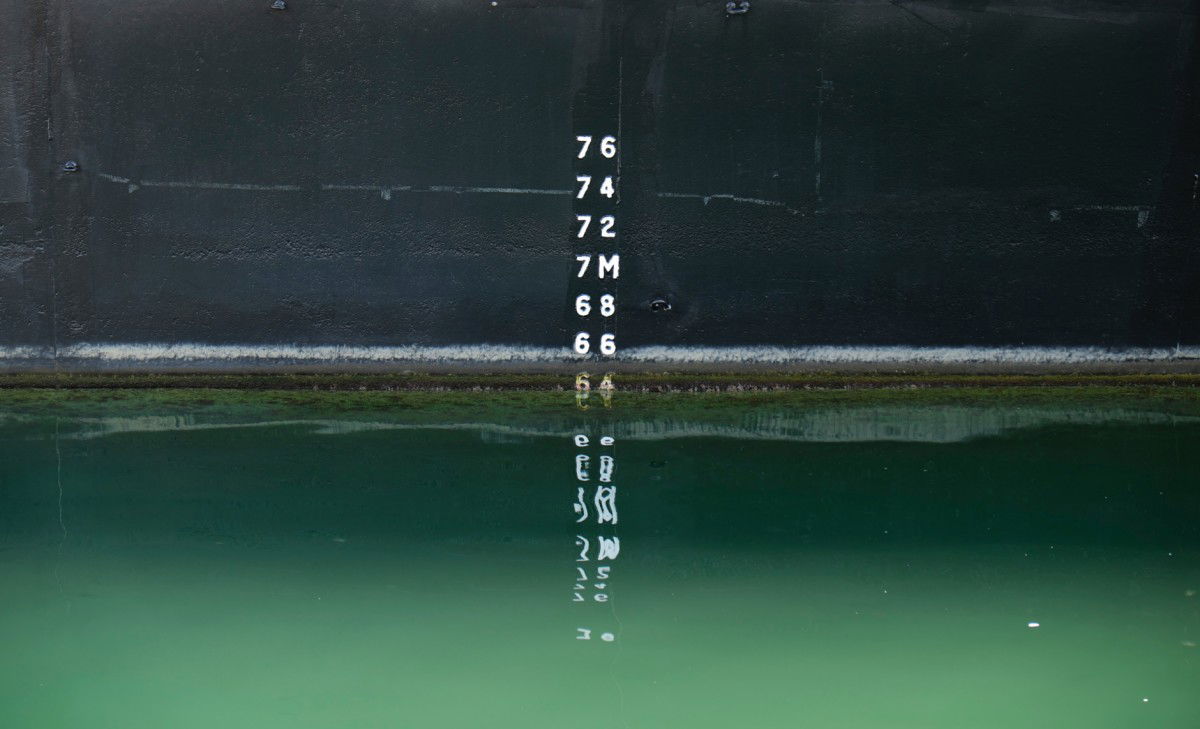
Waste Water Level Monitoring
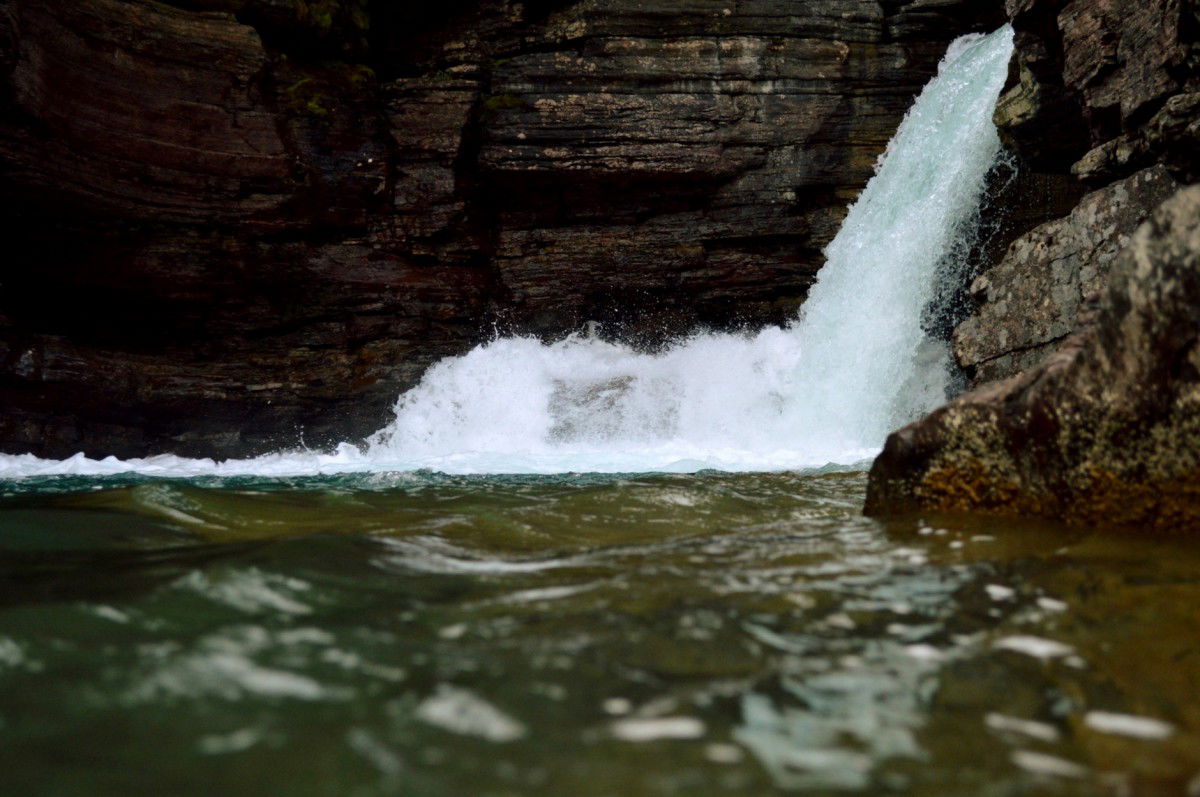
Continuous Level Measurement

Avoiding Pump Failures
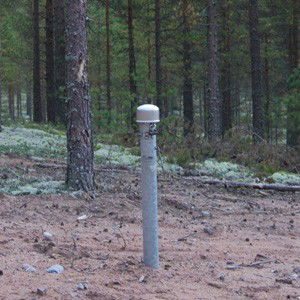
Wireless Groundwater Monitoring System
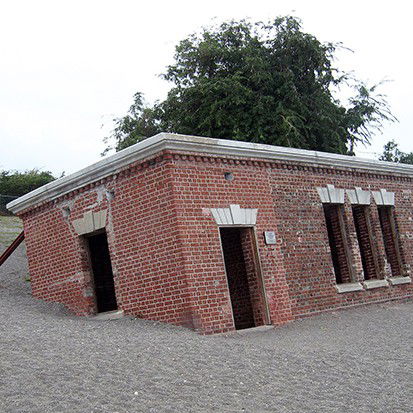
Cone Penetration Testing
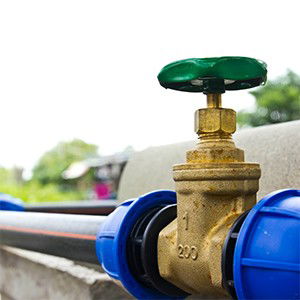
Water Consumption Monitoring
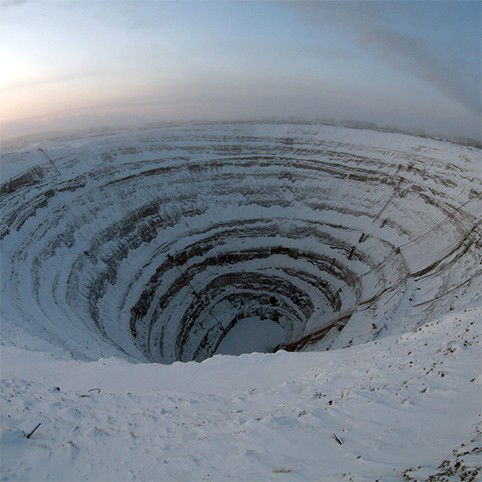
Water Monitoring in Open-Pit Mining
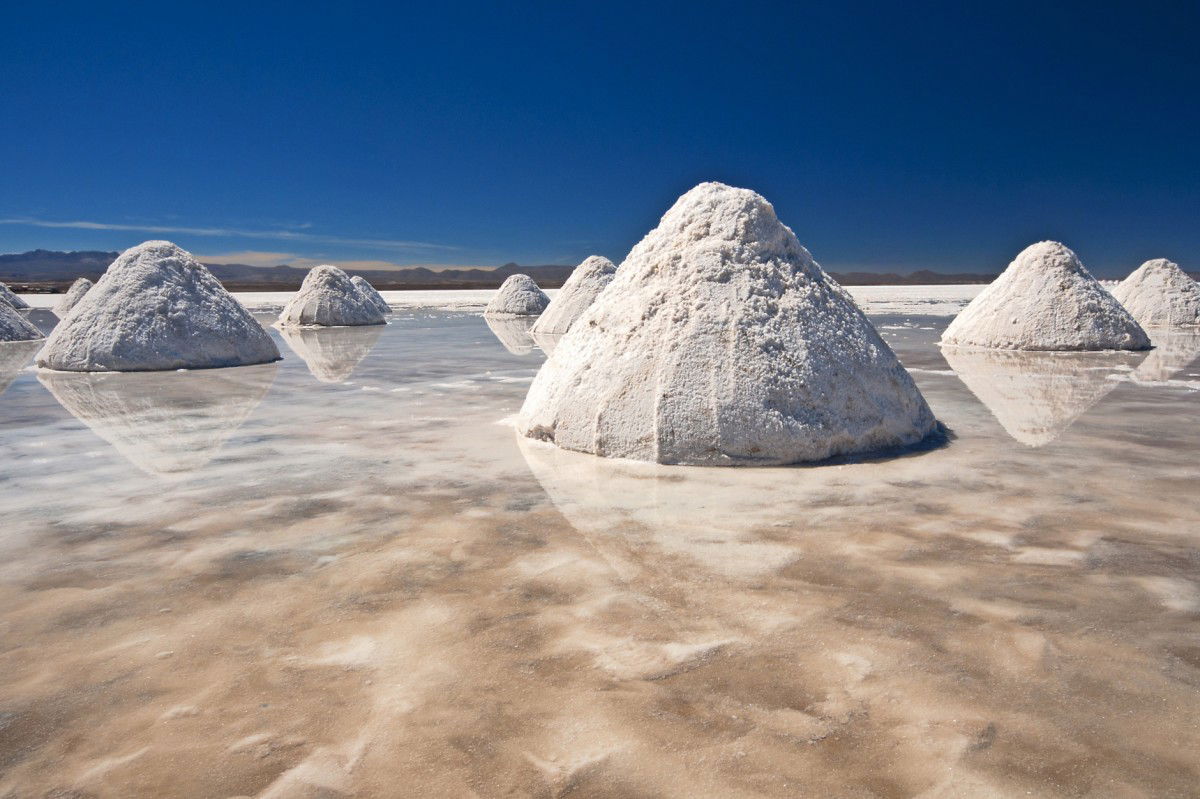
Lithium Brine Production
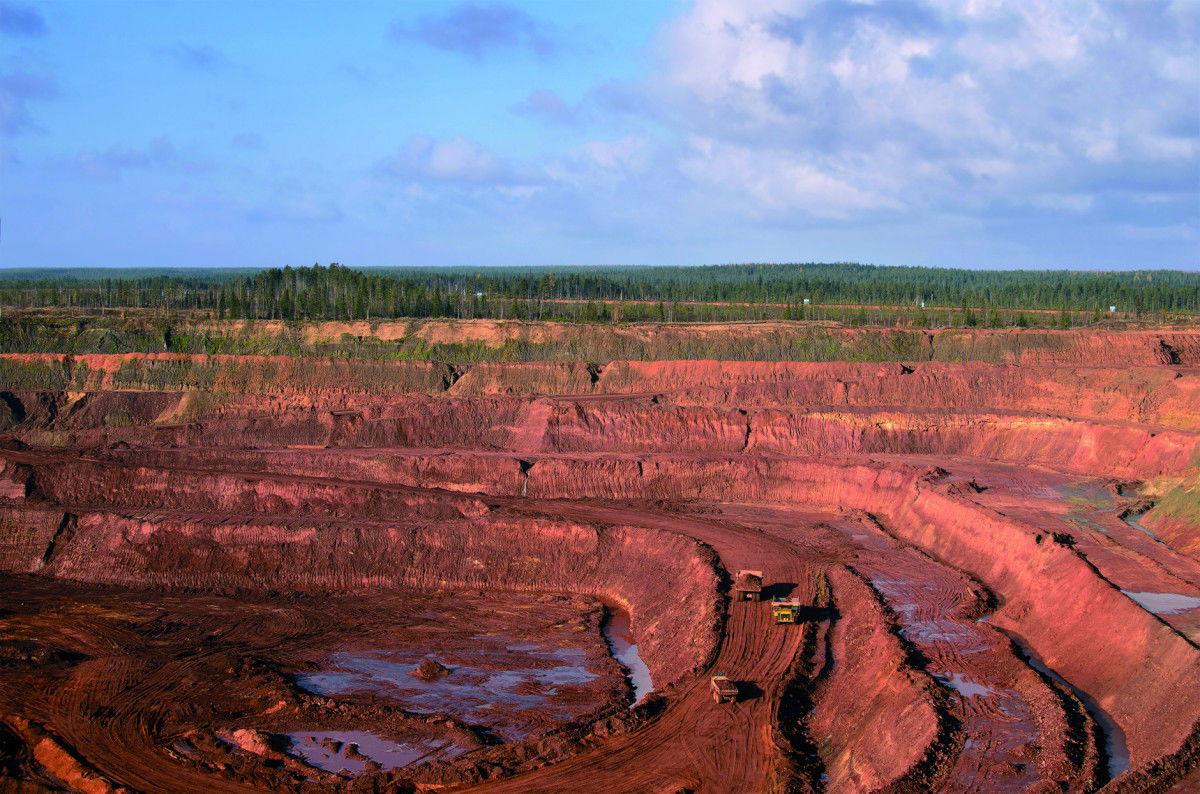
Dewatering a Diamond Mine
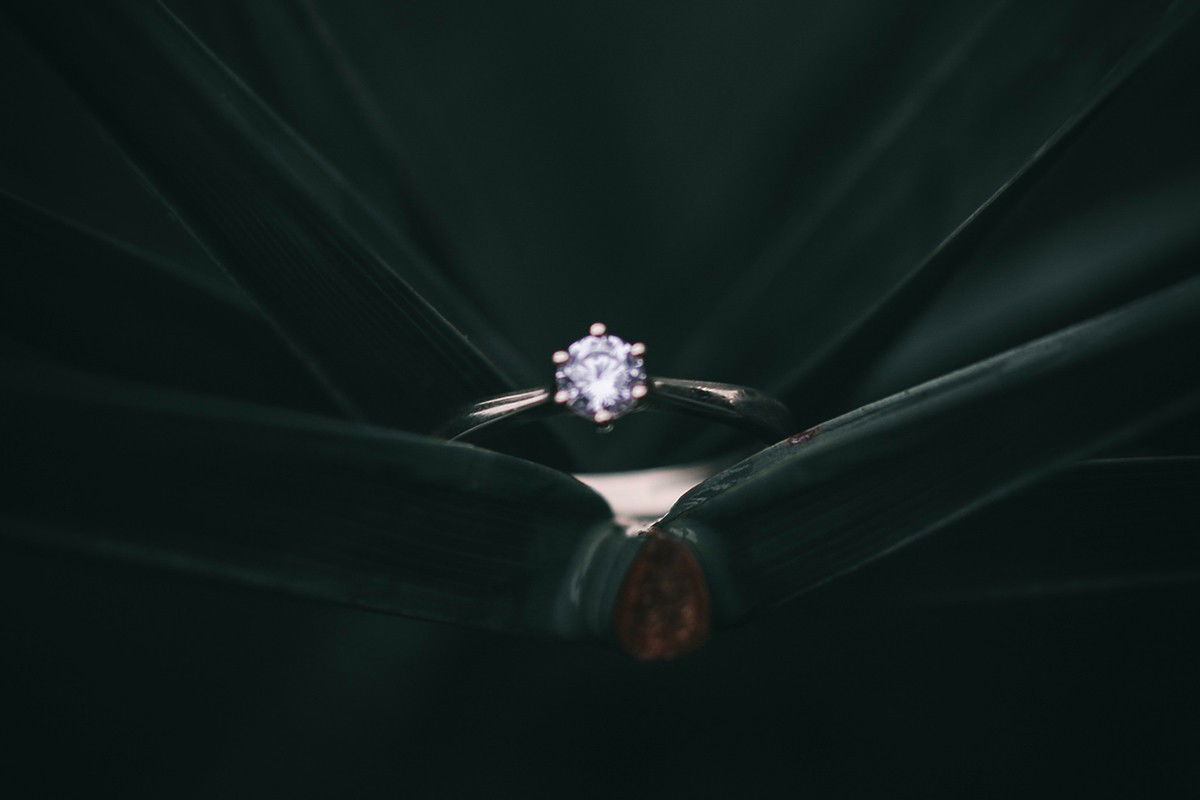
Mining in a Diamond Deposit
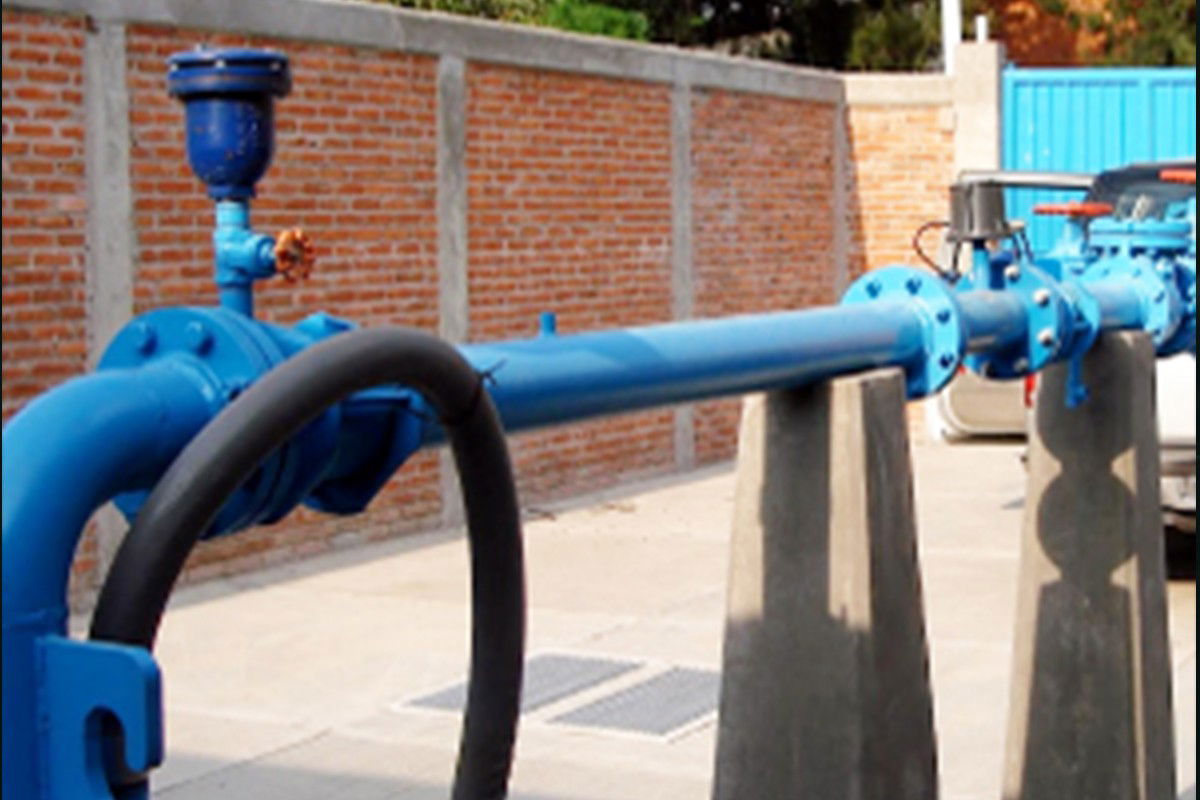
Water Wells Level Measurement
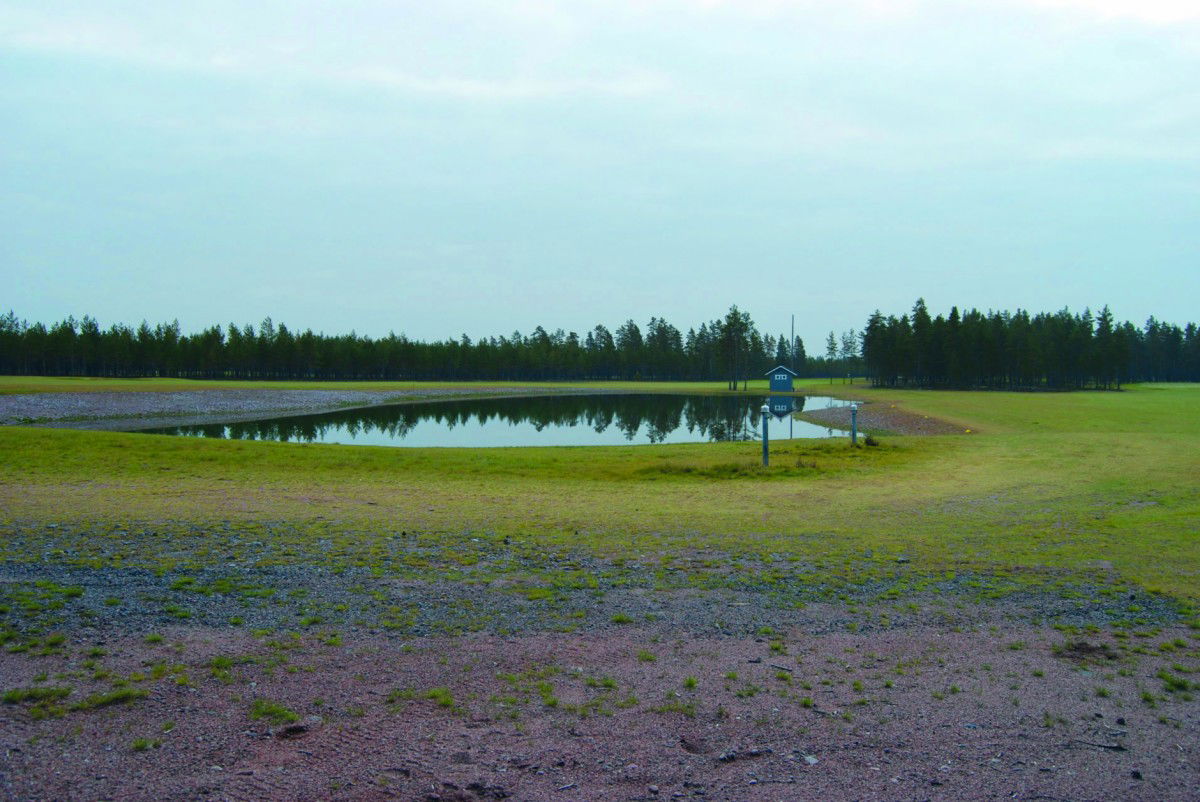
Groundwater Level Measurement
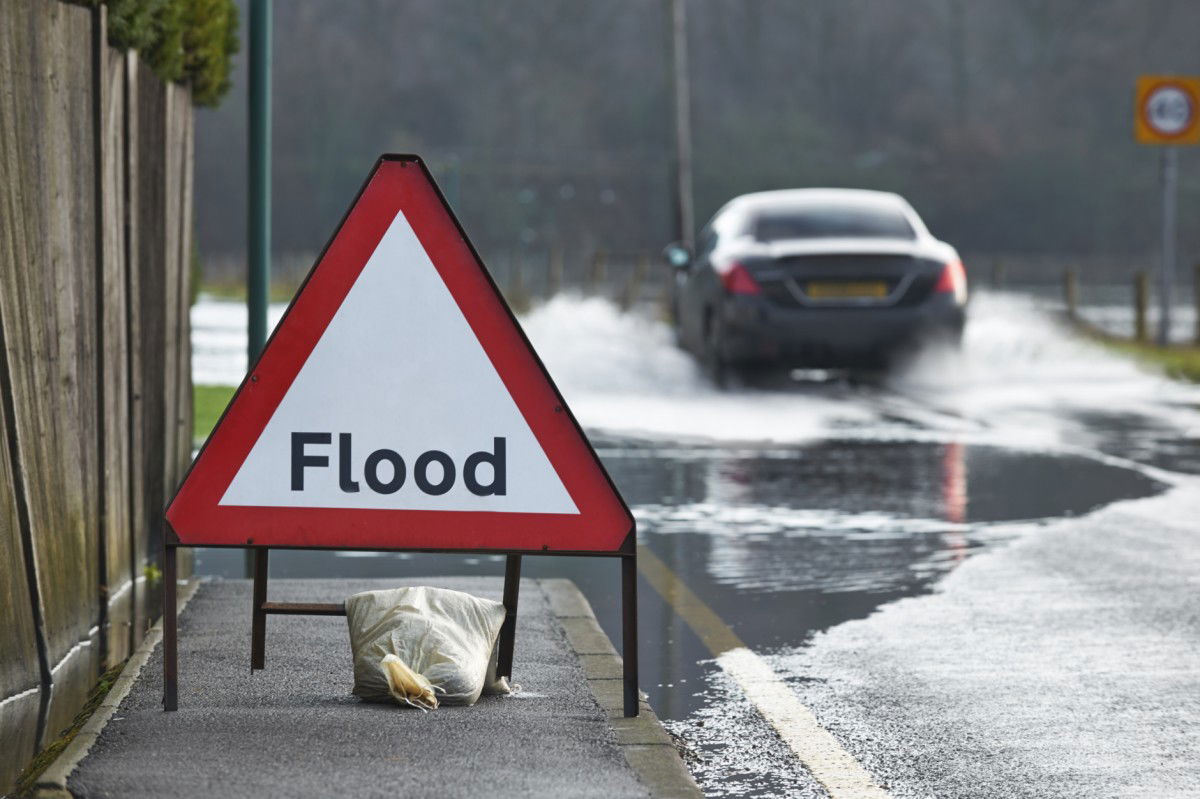
Automatic Flash Flood Warning
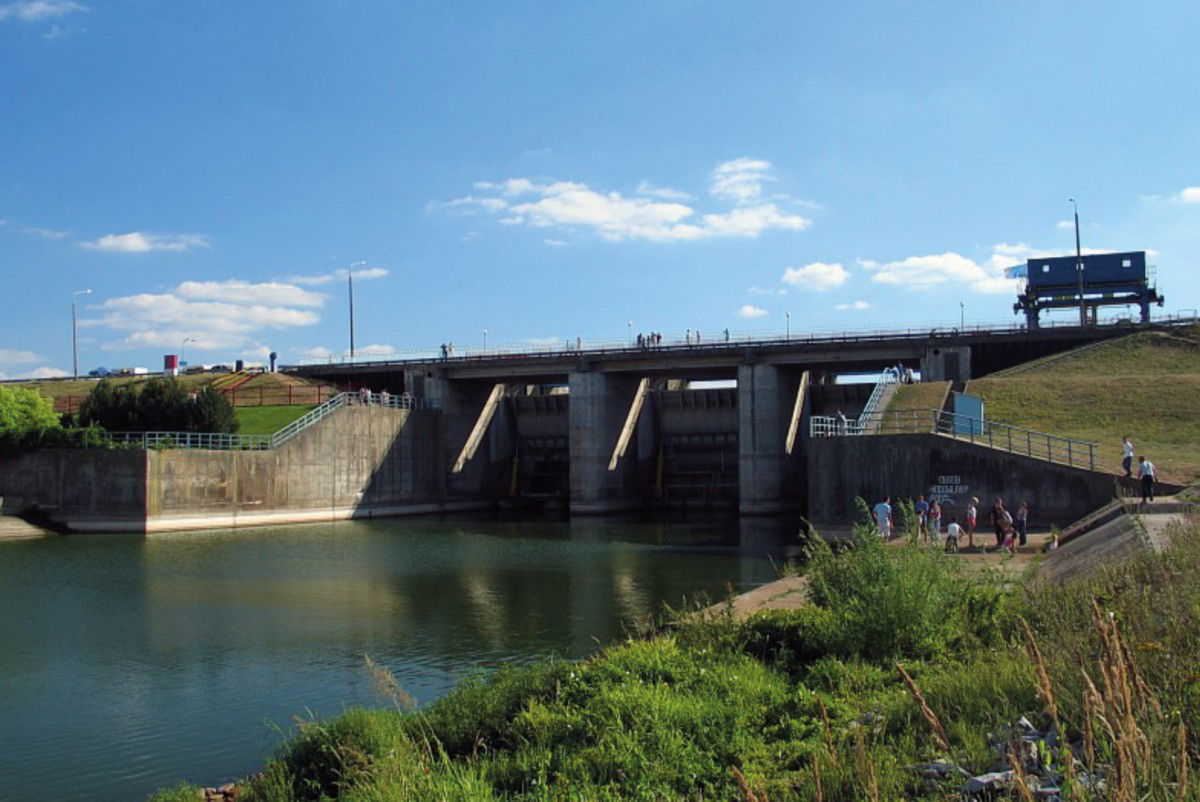
Dam Water Level Monitoring
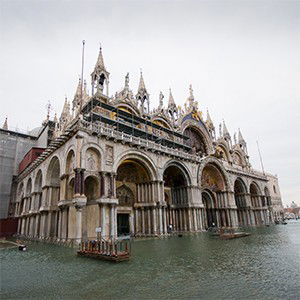
Keeping Floods at Bay
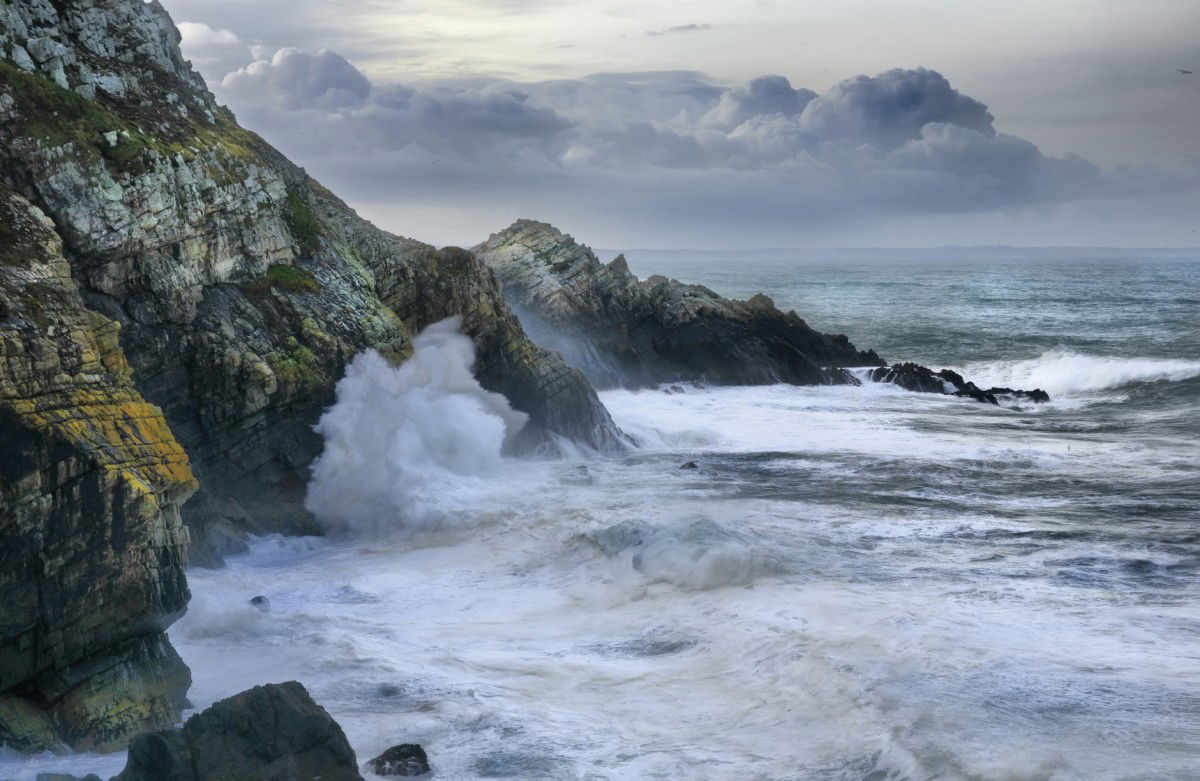
Monitoring Territorial Waters